YETI
The YETI drone has been in development since 2022 and has undergone extensive research, development and testing in both controlled and industrial environments. The YETI is based on a scaled-up YACOB DIAB system with the YETI being larger in all aspects, however, it uses the same trusted core electronics as the YACOB. The YETI DIAB system consists of the YETI drone and the YEDO docking station
The Yeti is a fully autonomous drone system capable executing missions such as surveillance patrol, inspection, mapping, logistics and transport.
Modules
Modules
Docking station: YEDO
This is an air-conditioned environment that protects the drone from meteorological conditions and other environmental factors. The ground station is used to exchange data, perform wireless charging and to house the drone in stand-by-mode for the next mission. The ground station also serves as the base station for communication with the YEDO. The ground station has an extendible funnel as shown in the following picture, from this funnel the drone will take off and land. This funnel has a special shape and a location beacon that together ensure that the drone lands autonomously in the correct orientation.
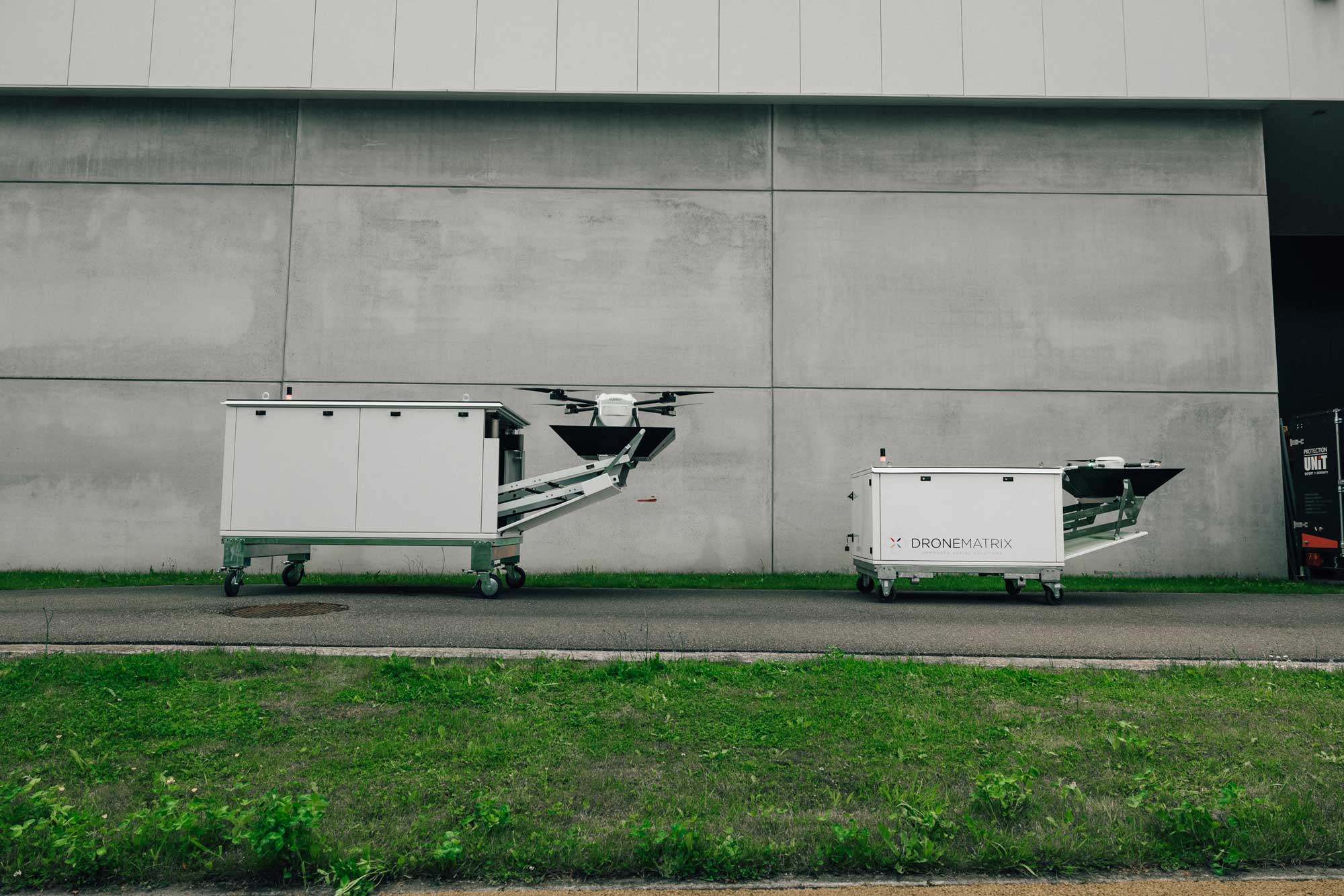
YETI has the ability to fly autonomously and gather data in the operational domain. Modular payloads and software, such as a high-resolution camera, infra-red camera, multispectral camera or sniffer sensors make this a truly versatile system. Live data is streamed to a dispatch centre or a dedicated monitor and the drone can perform in a swarm of several others if redundancy is needed.
The base station is the launching, landing and communication hub which houses and charges the aerial robot. This enables the drone to be piloted at a distance, where it can also be charged and transfer crucial data. The docking station is connected to a weather station and fog sensors to evaluate if a safe flight can take place.
Operational software environment, ARWS (Aerial Robotic Work System) acts as the digital enabler for the drone. This is the fully interoperable mission control centre where orders can be tasked, information can be gathered and communication can be facilitated for the customer and UTM.
The YACOB drone is the flying part of the complete YACOB DRONE SOLUTION.
The drone is connected to a physical ground station for several reasons:
- Protection of the drone against weather, climate, and environmental influences such as:
- Temperature: The YADO stabilizes the inside temperature to guarantee a perfect operational environment for drone, electronics, sensors, power supplies, power charging systems, communication systems, and computer processing systems. A HVAC (Heating, Ventilation, and Air Conditioning) unit is used to stabilize the temperature between 20 °C and 25 °C. When the outside temperature is colder, the unit will heat. When the outside temperature is warmer, the unit will cool.
- Rain, snow, UV, and dust: The YADO protects the operational systems against rain (water, humidity, fog = microscopic water particles), snow, ultraviolet light, interferences (cage of Faraday), and dust. The protection against touching and penetration of objects and the protection against moisture of the docking station corresponds to an IP value (International Protection Rating) of 43 (IP 43). This means that the docking station is protected against contact with a tool and against the penetration of solid objects larger than 1 mm. The docking station is protected against contact with a wire. The YADO is splash proof, which means that the unit will not be damaged when sprayed (10 l/min) at an angle of -60° to 60°.
- Wind and wind forces: Around the YADO a special wind fencing system is built to reduce the effects of strong wind (gusts) during take-off and landing.
- Human intrusion: The fencing, the YADO and the external camera form a physical barrier against intrusion, theft, and misuse.
- Animals and insect intrusion protection: Animals and insects find the environment of the box an interesting place to nest and breed. Therefore, the possibility to penetrate through openings are blocked physically and electronically.
- Remote control and management: Important to know is that all measurable factors as described above are monitored live and in real time by a monitoring help desk system whereby many processes are automated to meet the described parameters of operational use (pre-flight checks, in-flight checks, and post-flight checks).
A key advantage of a YACOB is that it allows operations without human intervention.
Therefore, the YADO has a set of functionalities:
- Launch positioning: Moving the drone exactly outside the box on the perfect height to launch the drone. This is made possible by a movable arm that brings out the platform. This movement is driven by 1 robust motor controlled by a PLC. This PLC is connected in real time to the ARWS (Aerial Robotic Work System), a web application which manages the drone installations.
- Rest positioning: When the drone is airborne, the YADO closes itself for reasons explained above (protection).
- Landing positioning: When the drone returns to the YADO installation the communication between the YADO and the drone starts the landing procedure by opening the box, setting the landing platform into position, and giving signals by infra-red lights to position the drone into the landing funnel. The infra-red lights give positioning to the optical (IR) camera built in the bottom of the drone to lead its landing maneuvering. To guide the landing of the drone, a special LiDAR (bottom) and the GPS data feeds the flight computer with e.g., the altitude so it can execute this landing action. Once landed, the drone shut its engines off and the landing platform is pulled back into the box. The exterior door is locked automatically.
- Remote control and management: All parameters relating to these procedures can be observed in real time via the docking station's telemetry, as well as being consulted historically. The video streams can be viewed in real time with low delays (400 msec) via the ARWS platform.
- Redundancy and fail-over: If there are any errors in this procedure due to a technical failure (mechanical, electronic, or electrical), a human failure (misjudgment), or an unpredictable weather change (storm, massive rain, snow, fog in combination with subzero temperatures, …), the drone will automatically move to an alternate landing site and land safely at this pre-designated location. While landing at this alternate location, a warning signal and strobe light will be turned on to indicate that an alternate landing is taking place. The drone will report itself to the ARWS system that the alternate landing has been initiated and upon touchdown will provide a safe landing notification.
For redundant and safe operations there are multiple communication systems built into the YADO, these are:
- Video stream inside the box to the ARWS system.
- Data communication to the RF communication antennas
- WiFi communication to the YACOB drones – upload and download wireless the data, telemetric, video/photo files, payload data, …;
- Fixed Ethernet connection to the internet, 4G/5G LTE, or Starlink communication (fail-over) for connectivity to the ARWS platform;
- Fixed connection to the weather station;
- Command and control communication from the ARWS to YADO systems.
- The YADO is a power supply system for the drone operations and the YADO operation:
- For the drone a wireless charging system is built in the box. This wireless charging system prevents bad contacts in case of charging the batteries of the drone. Two coil antennas are exactly positioned at the end of the receiving drone and start of the charge unit. This charging procedure is controlled by an automatic charging process and is being observed by the telemetric data transfer to the ARWS system. Parameters such as temperature, charging power, time, battery status, ... are observed in real-time and logged historically into the database for each YACOB unit per drone and per flight. Maintenance engineers can go back to the start-up of the system when required.
- Back-up (emergency) batteries are also installed in the YADO system when there is an electricity failure. The YADO stays up and running for 6 hours and can complete ongoing flight operations, communication with the drone and back-end ARWS system stays alive and safe. No further flights can be executed until the Drone Service Engineer gives clearance to re-use the YACOB installation.
DroneMatrix drones are capable of carrying a variety of sensors in multiple payload configurations. Sensors we have integrated into our systems:
- 4k RGB 20x zoom camera
- LWIR
- High definition mapping camera
- Multispectral camera
- Sniffer
- Hyperspectral camera
- Spectrometer
- Pyranometer
- Speaker payload
Life cycle Support
The Drone you bought yesterday will feel newer tomorrow.
We update our fleets and provide scheduled maintenance programs to ensure our drones are at the leading edge of technological advancements.
Maintenance training
We can train clients to become certified AirRobot technicians.
Upgrade support
We can provide the means to upgrade your fleet to the latest version as models evolve.
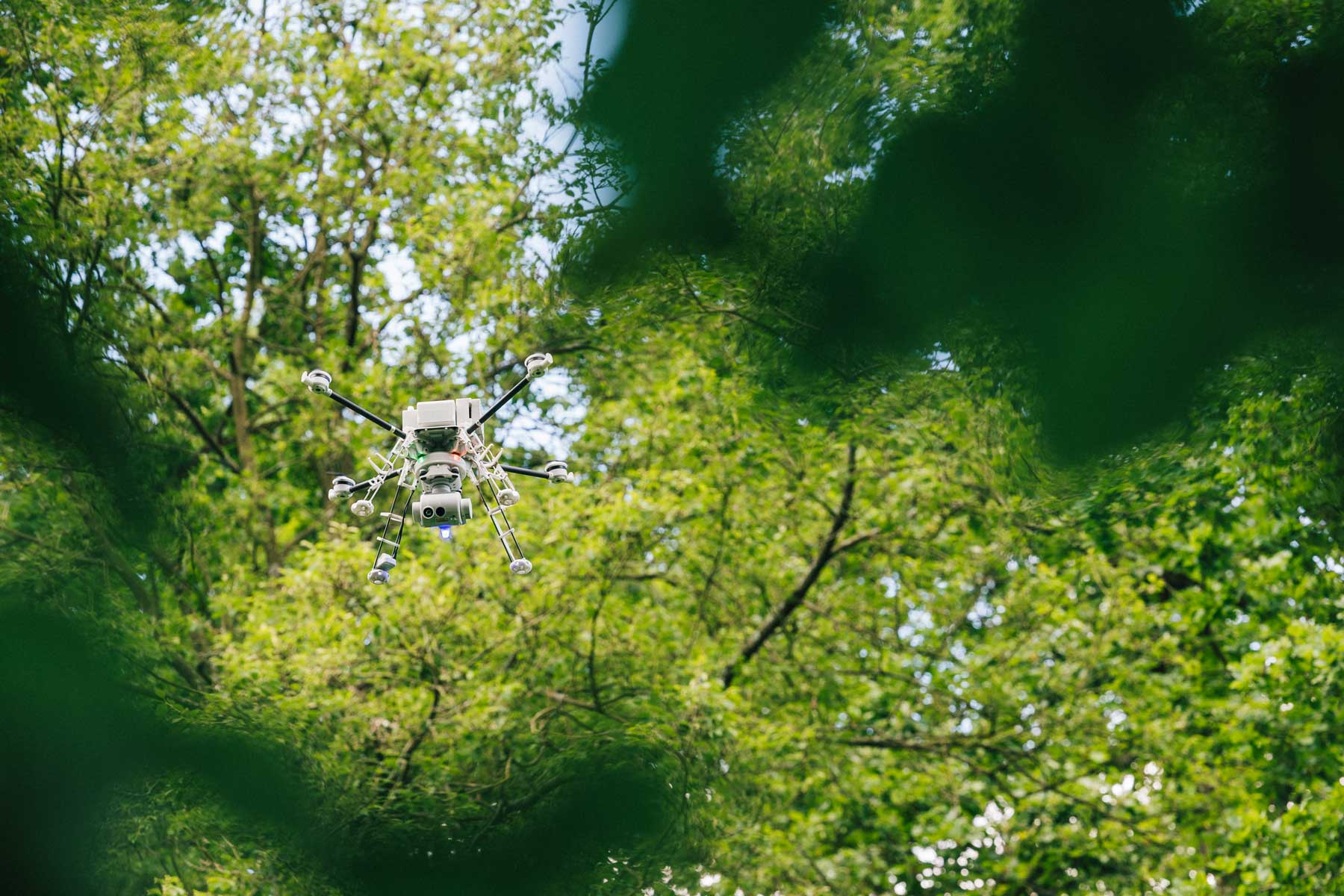
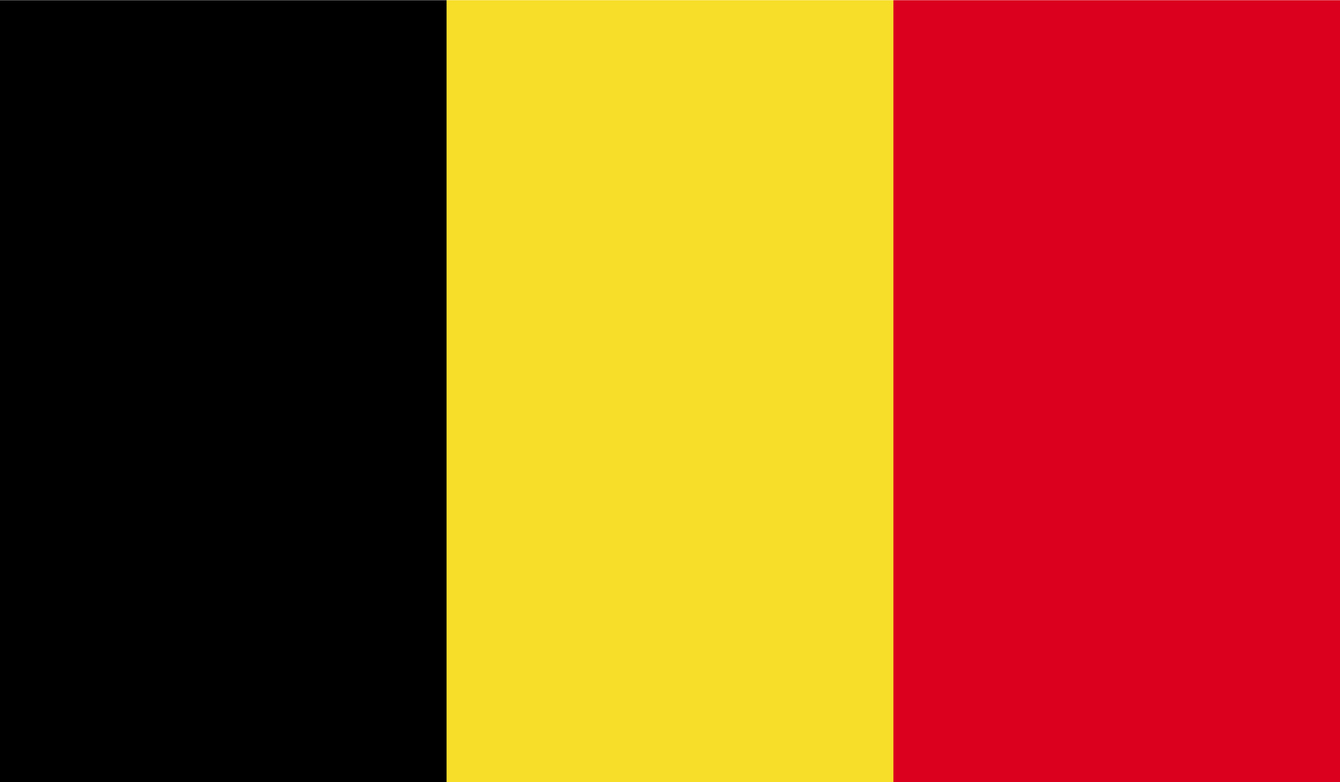
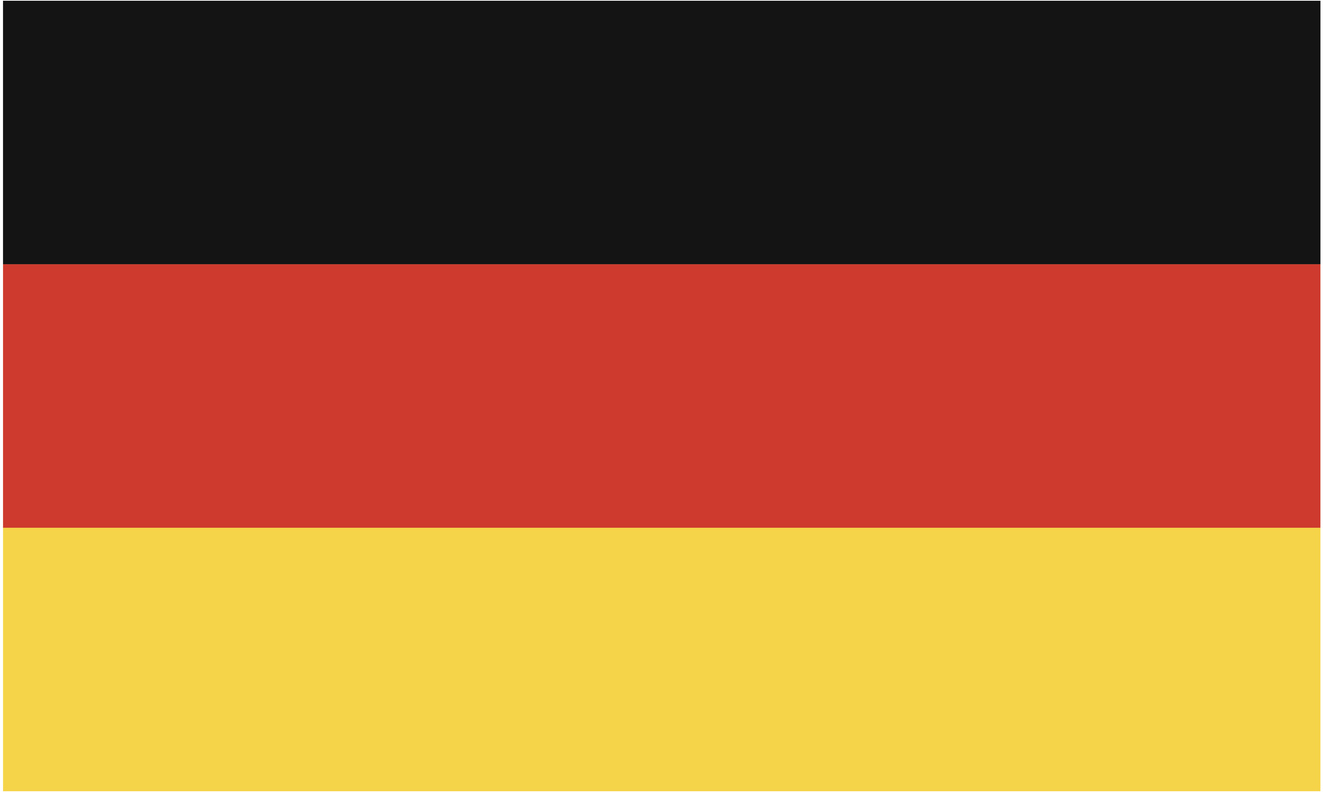
